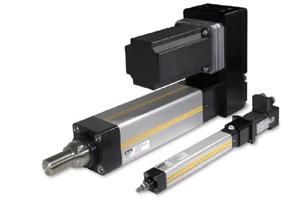
Servo Electric Press
The system is highly energy efficient, designed to substitute power consuming hydraulic and pneumatic presses. Combined with a wide choice of accessories, it offers many possibilities in a variety of applications. High Accuracy, speeds and repeatability features outperforms conventional Mechanical, Pneumatic and Hydraulic presses in all aspects. The Actuators, servo motors and drives used are from the Global leader in motion control technology - PARKER HANNIFIN INDIA PRIVATE LIMITED.General Features:
- 0.1% max. Full scale deviation in force
- Control panel with HMI preloaded with press fit software, no programming required
- 0.03 mm bi-directional position repeatability
- Safety features built-In
- Load - 5 Ton max.
- Supplied along with Load Cell
Enquiry
Better output product quality compared to conventional presses
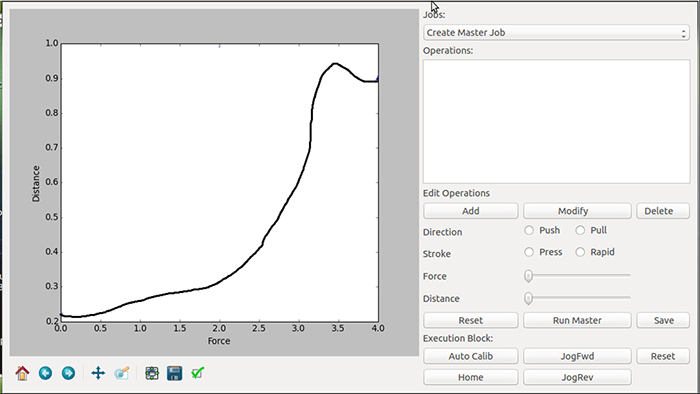
Software features:
- One touch auto calibration setup
- Master component teach / save capability up to any number of components
- Force vs Displacement plot
- Configurable component quality check function w.r.t master
- Data logging and Historical Trending of plots
- Modularity / Extendibility of multiple press systems from single software
We also offer press with work station bench on request
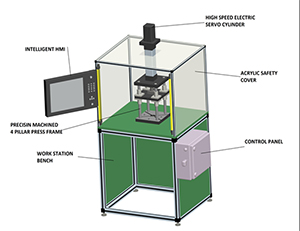
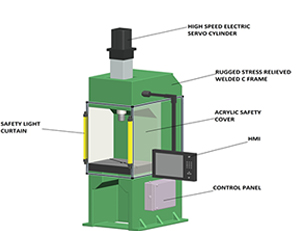
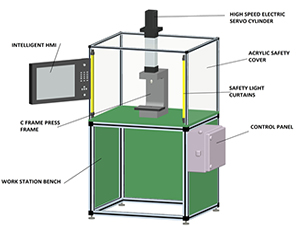
Variety of Applications
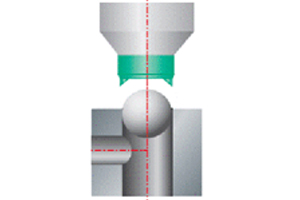
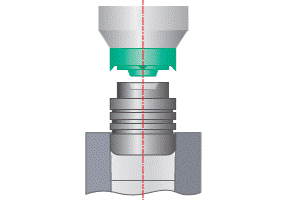
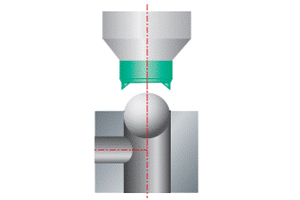
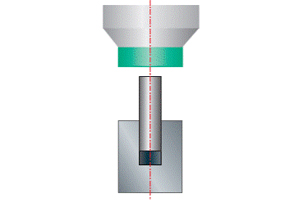
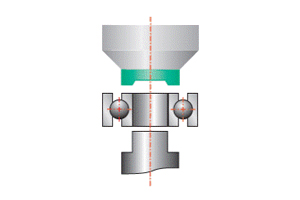
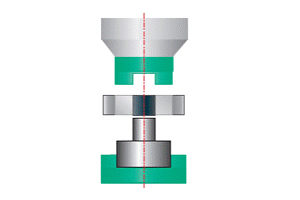
Few of our Installations
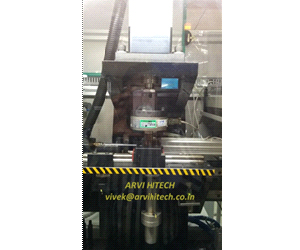
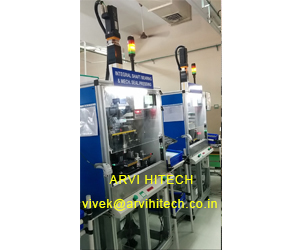
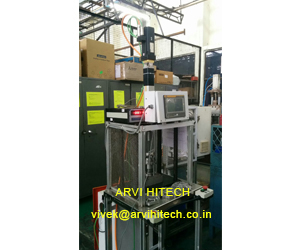
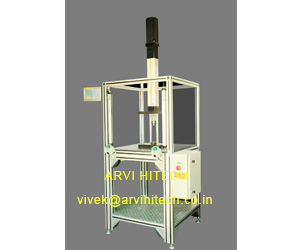
Success Story - PRICOL
Customer required high precision / tolerance press with closed loop force control for automotive component press. We were able to prove rapid movement and slow speed movement during press. The speed and position values could be dynamically changed by sending values from PLC to Press controller objects. Hence the same press is used for different sizes and variety of components just by changing the array objects. Closed loop force control feedback is also achieved using an external load cell fixed on to the press bed.
Success Factors | Customer Value |
High repeatability ensures and meets the quality requirements of the pressed component | 50% energy efficient compared to hydraulic presses. |
Closed loop configurable position and force control. | |
Same unit can be configured for different press components. | |
Local repair/ service support. | |
Local programming / commissioning support. | |
Control from any third party Master PLC gives more flexibility and independence. |
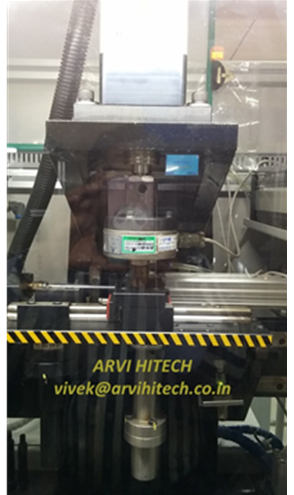
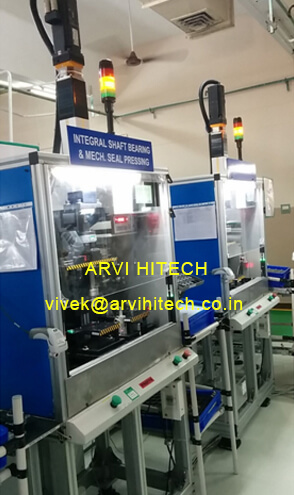
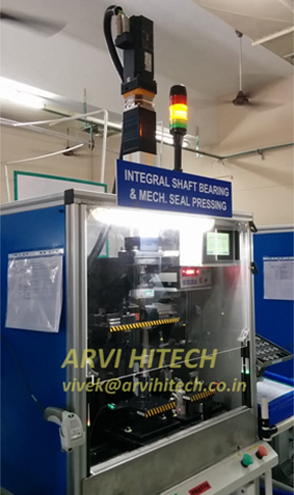
Success Story - Lucas TVS Pondicherry - Bearing Press
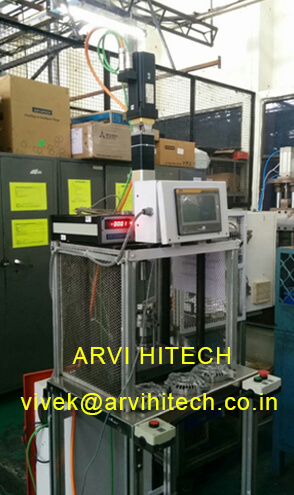
Success Factors | Customer Value |
Precise position control which is essential for output product Quality control. This was not possible with existing hydro/pneumatic and hydraulic presses. | 50% energy efficient compared to hydraulic presses. |
Force vs Displacement plot functionality enables customer to identify root cause in rejected components. | Same unit can be configured for different press components |
User set tolerance band for force vs displacement curve. | Local repair/ service support |
Multiple types of components can be pressed using the same system. One click component select from software. | Safety features built-IN. |
Automatic teach mode when adding a new component | Logged values of Force vs Displacement can be saved for future reference with Part name, date and time stamp. |
saves enormous time comparing to adding the component Force, displacement data manually. |
SERVO PRESS vs HYDRAULIC /PNEUMATIC / HYDRO PNEUMATIC PRESSES
SERVO PRESS | HYDRAULIC / PNEUMATIC/ HYDRO PNEUMATIC PRESS |
Closed loop control. | Open loop control |
Interfacing with front end is easy, comes with software package. | Front end is not applicable. No software. |
High cycle speed | Low cycle speed |
Full press capacity at full stroke Length | Full press capacity is not possible at full stroke Length |
Force control is precise and software configurable | Force control not possible. |
Position control is precise and software configurable. | Position control not possible. |
Different press motion/force profiles can be achieved. | Profile Changing is not possible, fixed profile. |
Additional features can be added with the help of program.Example: field bus communications, control sequence changes. | Additional features not possible. |
80 % Energy efficiency. | Only 25 to 30 % Energy efficiency due to increased sizing of motor and continuous running of power pack. In pneumatics, electrical to compressed air energy conversion efficiency is lesser than 25%. Hence 2 to 3 times more energy consumption compared to servo electric press. |
Tool protection is possible | Tool protection is complicated |
Good response time, 10 ms | Poor response time, 500 ms. |
Low maintenance. Only lubrication maintenance required approximately after service life. | Maintenance is high. Multi parts ( Filters, Valves, Fittings, Hoses) will be used in circuit and all parts should be maintained periodically. |